Environmental Engineering Reference
In-Depth Information
Table 11.6
Potential actions to increase the efficiency of industrial refrigeration systems.
Energy-Efficiency Action
Install high-efficiency compressor systems
Have variable speed drives for compressors
Use high-efficiency fan motors for condensers and evaporators
Install variable speed drives for fan motors running condensers and evaporators
Incorporate floating-head pressure control
Include liquid pressure amplifiers
Add subcooling units for refrigerant
Install evaporative condensers
Incorporate automatic purge for noncondensable gases
Operate compressors at nearly full capacity
Reduce cooling load
Conduct preventive maintenance
Recover heat
Screw
needs between 0.18 and 0.22 kWe/kWr.
●
Centrifugal without VSD
(variable speed drive) 0.18 to 0.22 kWe/kWr (COP 5).
●
Centrifugal with VSD
uses between 0.098 and 0.17 kWe/kWr (COP 5.5-10) (“Energy effi-
ciency best practices guide, industrial refrigeration,” 2009).
●
Electric motors that drive the condenser- and evaporator-fans have small power in com-
parison to compressors, but they operate constantly, and in most cases, the operational load is
lower than the maximum design load. For these reasons, condensers and evaporators benefit
when high efficiency motors equipped with VSD are installed to drive their fans.
Floating-head pressure control is generally a standard feature in new refrigeration systems,
but it also can be retrofitted to existing ones. Floating-head pressure control regulates the
pressure in the condenser according to the conditions of the environment. When outdoor
temperatures are low, the head pressure can be reduced while maintaining the refrigeration
output constant. This action decreases the work executed by the compressor, which translates
into energy savings and life extension of the compressor (Whitman et al., 2004).
Liquid pressure amplifiers, which are normally used in conjunction with floating-head
pressure systems, are small refrigerant pumps that increase the pressure of the liquid refriger-
ant once it leaves the condenser to reduce loss of capacity at low-head pressures. The use of
liquid pressure amplifiers allows operation at low-head pressures, which translates into a
lower need for compressing work and less energy consumption in the net balance. However,
the benefits of these devices are sometime controversial because it is claimed that the reduc-
tion on energy consumption is marginal (Reindl and Hong, 2005).
Significant reduction of energy consumption can be attained by subcooling the refrigerant
after it is condensed. This is achieved by using an oversized condenser (less effective) or a heat
exchanger after the condenser (more effective). The heat exchanger can be cooled by vapors
leaving the evaporator, by a secondary high-efficiency vapor compression system, or by an
external sink, such as air or water (Fig. 11.6) (DOE, 2005b).
In places where water scarcity is not an issue and the relative humidity of the region is
relatively low, then the use of evaporative condensers can produce an increase of efficiency
in refrigeration systems. Evaporative condensers use water that evaporates on the surface of
the condenser or uses a wetted filter to cool the incoming air before it contacts the condenser.
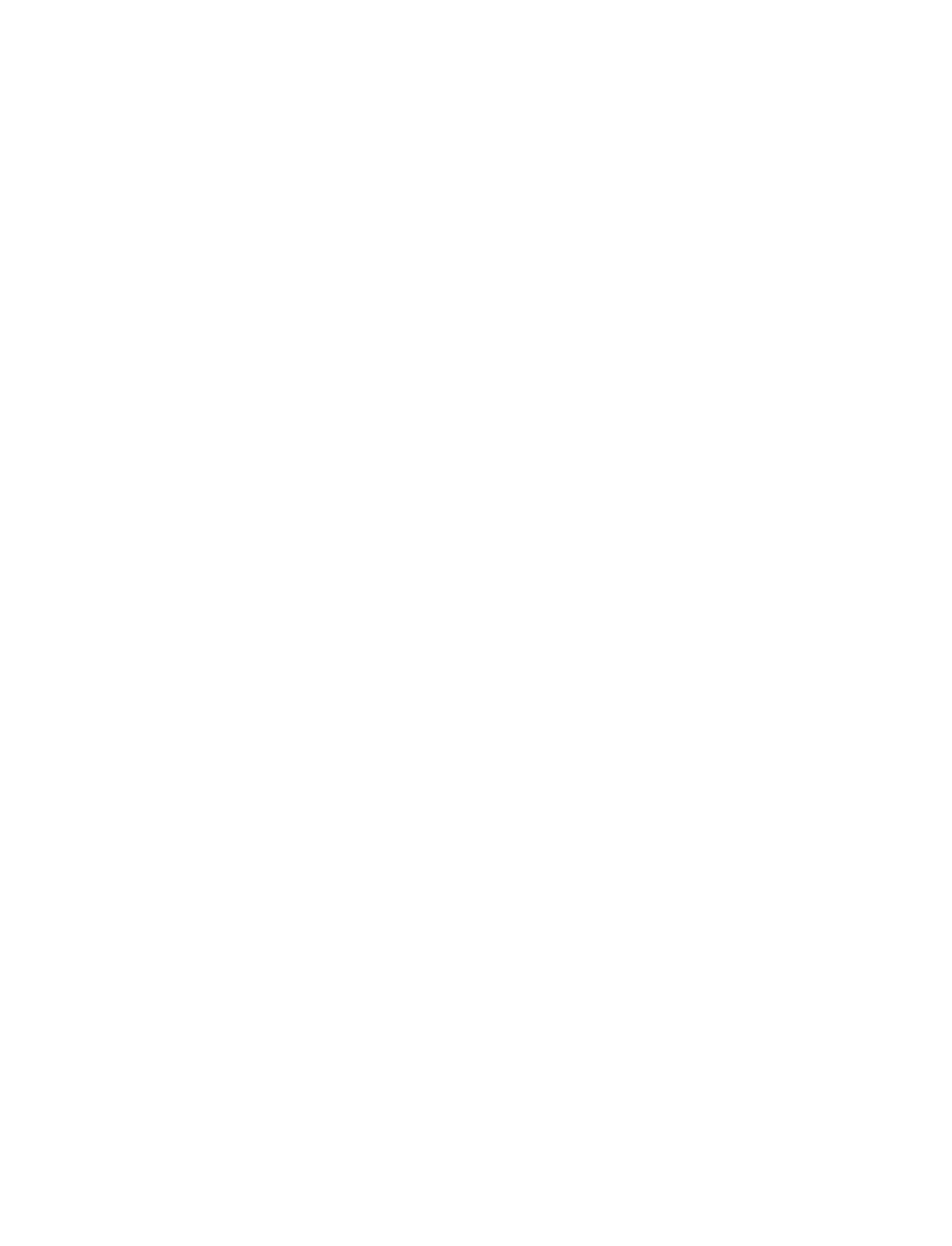





