Environmental Engineering Reference
In-Depth Information
al., 1993). Jain and Pradeep (2005) synthesized silver nanoparticles coated on common
polyurethane (PU) foams and used them in a drinking water filter. Nanoparticles were
found to be stable on the foam and were not washed away by water due to strong
interaction with the nitrogen atoms of PU. Morphology of the foam was also retained
after coating. Online tests were conducted with a prototypical water filter. At a flow rate
of 0.5 L/min, in which contact time was on the order of a second, the output count of
Escherichia coli
was nil when the input water had a bacterial load of 105 colony-
forming units (CFU) per mL. Combined with the low cost and effectiveness in its
applications, the technology may have large implications to developing countries (Jain
and Pradeep, 2005).
Figure 11.6
(A) HRTEM images of two different nanoparticles in a crystalline state,
which shows size ranging from 2 to 3 nm in size and possessing an icosahedral shape
(Gardea-Torresdey et al., 2003). (B) A plot of Ln[carbaryl] as a function of irradiation
time: (a) carbaryl only; carbaryl in the presence of AgY zeolite catalysts with various Ag
loadings: (b) 0.3, (c) 1.46, (d) 2.02, and (e) 2.42 wt % Ag (Kanan et al., 2003).
Chou et al. (2005) reported synthesis of fibers containing silver nanoparticles and
their antibacterial activities. These hollow fibers had a sponge-like structure and dense
inner and outer surfaces. After immersing in water bath for 180 days, the silver content
in the bulk of the hollow fibers decreased to 60% and the silver content on the surface
reduced to 10%; yet the silver fibers still showed antibacterial activity against
Escherichia coli
and
Staphylococcus aureus
(Chou et al., 2005). After permeating with
water for 5 days, the silver content in the hollow fibers decreased, and did not show
antibacterial activity against
E. coli
and
S. aureus
. This strongly indicates that silver
content must be periodically replenished after permeation. The proper range of AgNO
3
in the spinning solution for CA hollow fiber should be about 1001000 ppm (Chou et al.,
2005).
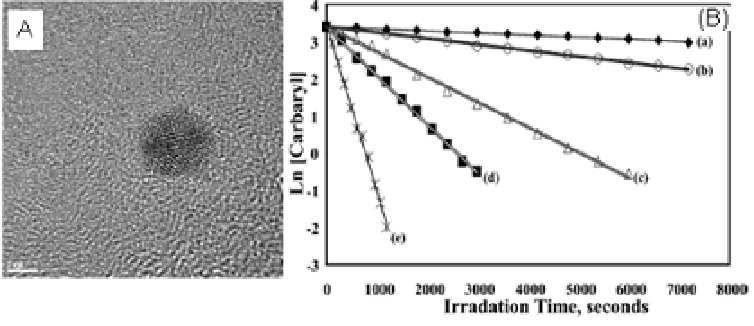
Search WWH ::

Custom Search