Civil Engineering Reference
In-Depth Information
Fig. 12
The schematics of OHP-BIPV/T module (Zhang et al.
2012
)
in mid-east area of UK) and operational conditions (i.e. 0.01 kg/m
2
s of mass flow
rate, 10 % of initial PV efficiency). The calculation models used are (1) indoor
simulator (IS) model for air-based PV/T (Solanki et al.
2009
); (2) IPVTS model
for water-based PV/T (Huang et al.
2001
); (3) PV solar-assisted heat pump (PV-
SAHP) model for refrigerant-based PV/T (Ji et al.
2008
); and (4) PV/flat-plate heat
pipe (PV/FPHP) model for heat-pipe-based PV/T (Zhao et al.
2010
). It is seen that
the air- and water-based PV/Ts are riskless and lower cost and therefore consid-
ered to be more practical systems for application. The refrigerant-based PV/T has
the advantage of low/steady working temperature, which could significantly
improve the system's solar conversion efficiency, whereas the heat-pipe-based PV/
T can extract heat from PV cells instantly, and if the operating temperature of the
heat pipe fluid can be adequately controlled, the solar efficiency of the system
could be significantly improved. However, these four systems have also found
their own disadvantages that are addressed in the Table
1
. To summarise: (1) air
type has poor heat-removal performance due to its low thermal mass and less
organised air flow; (2) water type remains increasingly growth of water temper-
ature over the operational period which results in poor heat-removal effectiveness
and low solar efficiency; (3) refrigerant type is difficult to handle in operation as
pressurisation and depressurisation are required in different parts of the system,
and risks of leakage and unbalanced refrigerant distribution remain high during the
whole process; (4) heat-pipe type retains the cost problem that may affect its wide
deployment in practical projects.
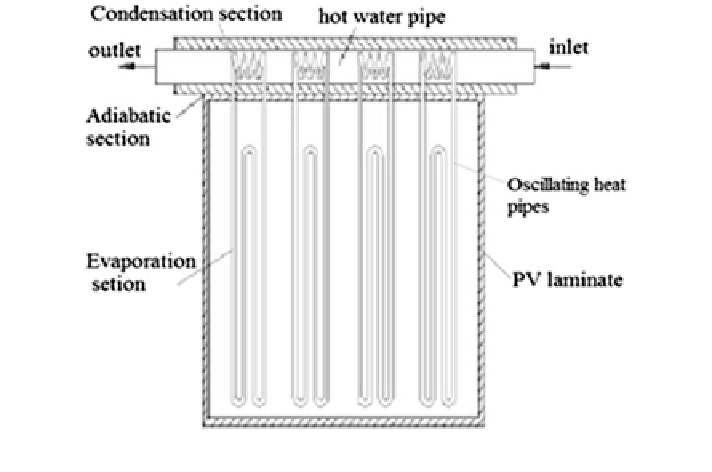