Geoscience Reference
In-Depth Information
To prevent sulfate attack, mortars made with sulfate-
resisting cement (
167
and
170
) may be used with bricks
manufactured with high soluble sulfate contents. They
may also be used for chimneys where sulfate from flue
gases can be deposited, or masonry in contact with
sulfate-rich soils or groundwater.
Ordinary Portland cement hardens to a grey colour
and, for aesthetic reasons, white Portland cement is
sometimes used as an alternative (
315
). Figure
316
shows
a case where white Portland cement has been mixed with
light brown, limestone fine aggregate to achieve an
overall buff-coloured decorative render. Figure
317
shows an example of joint mortar used between blocks of
Portland limestone masonry, which was intended to
match the buff colour of the limestone.
Modern Portland cement mortars may incorporate
pigments to provide a colour of the purchaser's choice
(
318
). They are mainly metallic oxides in the form of a
fine, inert powder and are often difficult to disperse
evenly throughout a batch of mortar. For this reason
pigmented mortar is best obtained as premixed lime:sand
coarse stuff or as ready-to-use mortar (Monks, 2000).
M
IX PROPORTIONS
For Portland cement-based mortars and renders, mix
proportions are usually determined by simple chemical
analysis involving acid dissolution, for example in
accordance with the BS 4551 method (British Standards
Institution, 2005a) or the ASTM C1342 method (ASTM
International, 2005b). These methods give quite good
estimations for mixes containing siliceous aggregate. Both
standards can cope with Portland cement:sand, Portland
cement:lime:sand, and masonry cement:sand mixes. There
is the disadvantage that carbonate aggregate particles
(limestone, marble, shell) will be dissolved away with the
binder giving incorrectly high binder content values.
However, estimation of the type and quantity of calcareous
aggregate made through the microscope can be used to
correct erroneous results of simple chemical analysis.
315
W
ORKMANSHIP
Poor workmanship is probably the biggest cause of early
mortar and render failure in new buildings and will, over
time, adversely affect the long-term durability of
masonry. Batching errors are more likely to occur with
site-mixed mortars, where inaccuracies in mix
proportions can result from deficiencies in the method
used to batch the ingredients. Mortars must be well
mixed to achieve their potential strength and this
depends on the order in which the ingredients are loaded
into the mixer and the mixing time. Symptoms of
inadequate mixing include weak/friable mortar and the
presence of unmixed lumps of cement (
319
). These
symptoms may also indicate the use of stale cement.
Over-mixing of mortar will introduce too much air into
the mix, in the form of entrapped air voids that will
reduce the hardened strength and durability.
Air entrainment can improve the frost resistance of
both freshly laid and hardened mortars. BRE Digest 362
(Building Research Establishment, 1991) recommends air
contents of between 10% and 18% for this purpose. Figure
320
shows an example of an air-entrained mortar. Too
much air entrainment can lead to poor durability, low
compressive strength, and poor bond strength (
321
).
Excessive air entrainment is a regularly seen defect on
315
Close view of a partially hydrated white Portland
cement grain in a decorative render. The grain consists
of calcium silicates with no interstitial ferrite; PPT, ×300.
316
316
Decorative (buff-coloured) render comprising
mixed crushed brown limestone (light brown) and
natural quartz-rich sand fine aggregate, bound by a
matrix of white Portland cement (black). An unhydrated
cement grain is seen in the centre of view; XPT, ×150.



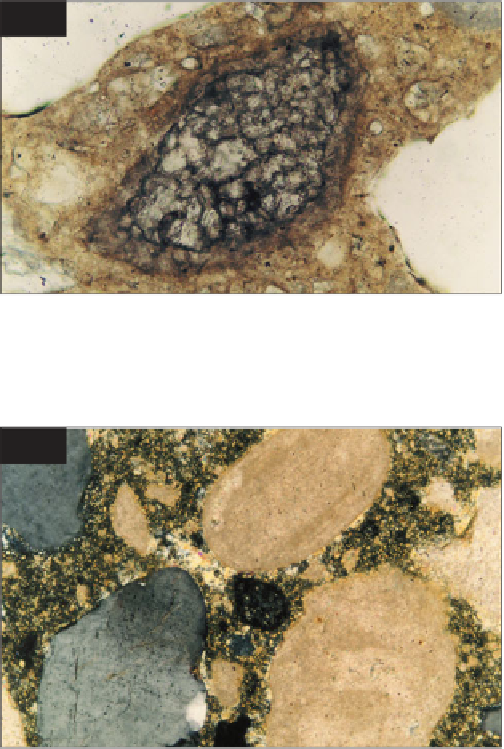