Civil Engineering Reference
In-Depth Information
Fig. 4.22
Power relationship
for exponential values as a
function of current density
the material. Combining the developed relationship with the traditional power law,
it is postulated to characterize the flow stress of the electrically deformed material
as a result of its initial nominal current density of over the range of strain tested.
4.5.1.2 Empirical Relationship
Using the methodology from the
Relationship Development
section, the resulting
model for the upsetting flow stress is predicted using:
σ
predicted
=
K
′
ε
n
ε
m
exp
−(ε −
c
)
B
A
(4.9)
where,
σ
predicted
is the predicted flow stress with the application of electricity,
K
′ is
the strength coefficient,
ε
is the strain, n is the strain hardening exponent,
ε
is the
strain rate,
m
is the strain rate sensitivity exponent,
Φ
is the current density, and
A
,
B
, and
C
are material specific constants for this model. Also, when considering the
current density, since the current varies as a function of strain, the current density
in this model was considered to be decreasing. Neglecting barreling, the instanta-
neous current density during the test can be described by:
Ih
A
o
h
o
=
(4.10)
where
Φ
is the current density,
I
is the current,
A
o
is the initial area of the specimen,
h
o
is the initial height of the specimen, and
h
is the instantaneous height of the speci-
men during the testing. Thus, as the test progresses, the current density decreases
as the specimen decreases in height. One important fact to note is that the current
(
I
) during the test is assumed to be constant. However, since the current provider
for this setup supplies a constant voltage, the current is dependent on the resistance
of the system, simply using Ohm's law. As a result, the resistance of the system is
dependent on the temperature, geometrical changes, and microstructure changes of
the specimen. As the temperature is increased, this causes the resistance to increase
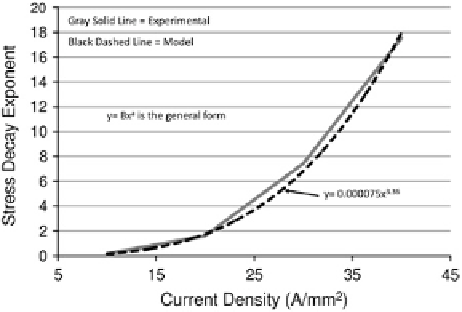