Civil Engineering Reference
In-Depth Information
Fig. 4.18
EEC profiles
(CD15, 12.7 and 25.4 mm/
min) [
1
]. The mechanical
and thermal EEC profiles are
similar for each respective
speed. Additionally, the
slower speed produced a
higher EEC value at this
particular current density
0.4
0.35
0.3
Mech. (12.7)
Therm. (12.7)
0.25
0.2
0.15
0.1
Mech. (25.4)
Therm. (25.4)
0.05
0
0%
25%
50%
75%
100%
% Stroke Completed
Fig. 4.19
EEC profiles
(CD25, 12.7 and 25.4 mm/
min) [
1
]. The faster
deformation speed produced
a higher EEC value when
coupled with this particular
current density
0.3
0.25
0.2
Mech. (25.4)
Therm. (25.4)
0.15
0.1
Mech. (12.7)
Therm. (12.7)
0.05
0
0%
25%
50%
75%
100%
% Stroke Completed
die speed (12.7 mm/min) is higher than the faster die speed profile after about
25 % of the desired compressive stroke is completed. This can be expected, since
previous works have proven the EAF technique to be strain rate dependent [
8
].
The EECs for a starting current density of 25 A/mm
2
are shown in Fig.
4.19
. As
was the case in Fig.
4.18
, both EEC calculation methods are consistent throughout
the entire compressive stroke for both the die speeds. For the case of current den-
sity of 25 A/mm
2
, the EEC for the die speed of 25.4 mm/min was on average 12 %
higher than for the case of 12.7 mm/min, with a maximum difference of 17 % at
the end of stroke. Please understand that the EEC is not solely based on the reduc-
tion in mechanical power, but that it is determined from the power reduction with
respect to the magnitude of electrical power input required to create that reduction.
4.4 EEC Profile Conclusions
The previous sections analyzed two methodologies for quantifying the EEC. An
experimental upper bound mechanical approach and a thermal analytical approach
were utilized to determine the EEC profiles. The conclusions from the previous
sections are as follows:















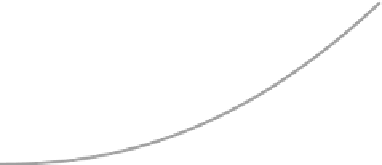













