Civil Engineering Reference
In-Depth Information
Fig. 11.38
Al2024-T4
EAM stress-strain tensile
profiles [
18
]. When the
electricity is applied to a
tensile deformation process
continuously (as is done
with compression tests), the
larger amounts of electrical
power will produce decreased
elongations. Hence, this is
why electrical pulsing is
performed on EAM tensile
processes
The conclusions from this work are:
• If electricity is applied continuously during a tensile deformation process, the
forces will be reduced; however, the achievable elongation will also be reduced.
• The difference in the specimen conditions throughout tensile and compressive
tests explains the reasoning for the continuously applied electricity causing a
detrimental effect on the tensile process. Specifically, the cross-sectional area
of the workpiece will increase in compression (the current density will decrease
over the test), and the cross-sectional area of the workpiece in tension will
decrease (which will increase the current density of the specimen over the test).
11.4.2.2 Benefits of Pulsed Electricity in Tensile-Based Processes
The previous experimental EAM work indicated that, when continuous DC current
is applied to a part during tensile or compressive deformation, the required flow
stress is reduced [
8
-
18
]. However, the effect of the continuous current on the max-
imum achievable elongation of the part was significantly different for compres-
sive and tensile loading. When performing compression-based deformation, it was
found that the application of a continuous current dramatically increased the mate-
rial's deformability. This was not true when performing tensile-based deformation,
however. When continuous electricity was applied during tensile-based deforma-
tion, it was noted that the deformability of the material decreased (Fig.
11.38
).
In subsequent studies, however, it was discovered that, when a pulsed current
(rather than continuous) was applied during tensile deformation, the maximum
achievable elongation was increased (rather than decreased as was true for contin-
uous). In a recent study conducted by Roth et al. [
19
], the effects of a pulsed DC
current on 5754 aluminum alloy, a widely used alloy for body panels in the auto-
motive industry, were investigated. This research involved developing an optimal
pulsing parameter in order to minimize the flow stress and maximize the material's
overall achievable elongation, thereby placing the material into its most workable
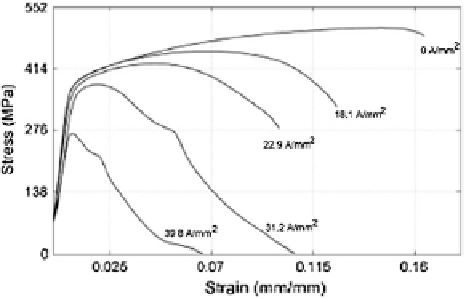