Civil Engineering Reference
In-Depth Information
Fig. 1.5
Superplastic forming. A part is heated to roughly two-thirds of its melting temperature
and formed to allow for great elongations and a formed part with very few residual stresses
for deformation are minimized. This process can be used to form complex shapes
because of the very low-forming forces; however, it also has its disadvantages.
First, the superplastic-forming process is only applicable for very fine-grained
alloys (less than 10-15 µm), such as some aluminum (5083-FG and 7475), titanium
(Ti-6AL-4V), and magnesium alloys (Mg-AZ31B). These small grains allow for
GBS (grain boundary sliding) to occur at elevated temperatures, which is the pri-
mary SPF deformation mechanism responsible for the huge elongation increases.
Another consequence of this process is that extremely slow strain rates must be used
(10
−
4
- 10
−
2
s
−
1
). Similar to the incremental-forming technique, the superplastic
technique may not be practical for many high-production manufacturing applica-
tions and can be classified as a batch-forming process. Neglecting the limited num-
ber of applicable materials and the slow strain rate that is required, this process is
capable of producing precise complex geometrical parts with little or no finishing
operations needed. Vehicle manufacturers, such as Porsche and Aston Martin, have
used SPF to form components for their low-production exotic cars.
1.2.4 Tailor-Welded Blanking
When using tailor-welded blanks (TWB's), different sheets of material (i.e., differ-
ences in material grade, thickness, or coating) are mechanically or automatically
welded together before the forming process [
18
]. This allows the manufacturers
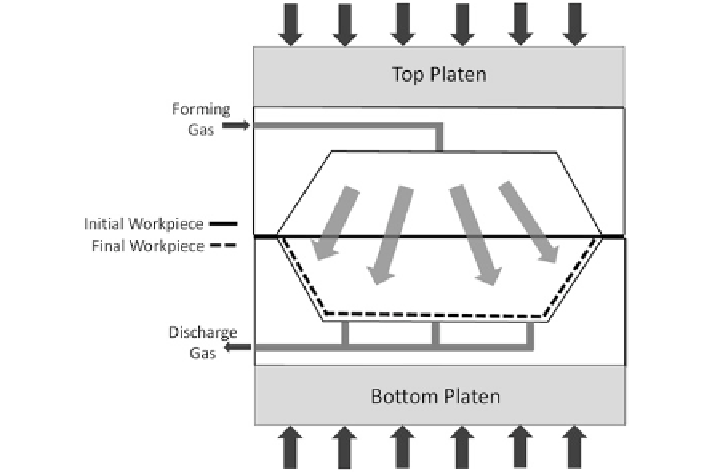