Civil Engineering Reference
In-Depth Information
Fig. 7.8
Thermal response for constant force forming tests. The surface temperature increases
rapidly at first, then decreases with time and deformation displacement [
1
]
In addition, the thermal surface response of the tests was recorded and the
maximum temperature of the sample with respect to time is given in Fig.
7.8
. As
the current is applied, the temperature drastically increases, and then, the rate of
change of temperature begins to decrease as the material reaches the desired force
set point (i.e., lower current level to maintain force). As the test continues, the
temperature follows the same trend as the electrical current which decreases until
the specimen fractures. The thermal response is presented here as this could repre-
sent another possible area for control. Specifically, the temperature during forming
could be controlled by modulating the electrical current applied if real-time tem-
perature data were available. A similar approach has been presented for stationary
heating using an electrical current before performing a Kolsky Bar test [
2
], but not
for forming during deformation.
As discussed previously, thermal gradients generated from the forming
boundary conditions (i.e., dies) create areas that undergo greater amounts of
deformation. Thus, these regions that are subject to greater amounts of defor-
mation are in a higher stress state. The stress profile presented in Fig.
7.6
is
therefore a mean stress prediction of the material based off of Eq. (
7.2
). The
strain and thermal gradient can be observed by examining the specimen geom-
etry and temperature as depicted in Fig.
7.9
. The current was applied just after
33 s and was discontinued at 414 s. Also, the peak temperature exists in the
center of the specimen and is lowest near the die regions, thus the deforma-
tion is highly localized in the center of the specimen. For a practical usage of
this technique, die design is a critical area to be further investigated such that
any thermal gradients would be minimized from the workpiece to the dies.
Overall, the complex mechanical and thermal relations for EAF required more
advanced models if it is desired to understand the localized stress and thermal
gradients.
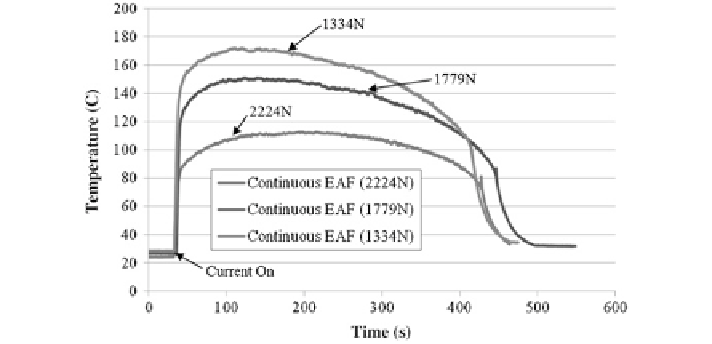