Civil Engineering Reference
In-Depth Information
Fig. 7.4
Control schematic using cRIO. The position, load, and current are acquired using an
analog input, and control is made using a signal voltage to the power supply through an analog
output [
1
]
(AI) on the cRIO. Additionally, the measured current (
I
measured
) is collected using
the AI on the cRIO. The cRIO interfaces with a computer, which also records ther-
mal data (
T
). The cRIO controls the power supply output (
I
) by applying a feed
voltage (
V
feed
) from the analog output (AO).
For the current supply to provide the correct output to the process, a feed volt-
age with a linear relationship was established. The feed voltage was used to com-
municate to the power supply to set the desired current output. Once the power
supply control was established, the LabVIEW software was modified to specifi-
cally include a PID control block. A PID controller is a general controller that cal-
culates an error between the set point value and the measured result. Using this
calculated error, the controller adjusts the process inputs to try to minimize the
error. The controller has three terms:
P
,
I
, and
D,
where
P
is dependent on the
present error between the actual state and set point,
I
is on the summation of past
errors, and
D
is the current gradient of error, estimated from the last two data
points. For constant force forming, three force set points were tested to show the
robustness of the control application.
The force results for constant force forming at 1,334 N (300 lb), 1,779 N
(400 lb), and 2,224 N (500 lb) are presented in Fig.
7.5
. As the control system is
turned on just after the material's yield point, the applied current quickly drives
the force to the desired set point. After reaching the desired set point value, the
controller is capable of accurately modulating the applied current to maintain con-
stant force forming until the specimen fractures. The physical reason for the oscil-
lations in the force response is not presently known. The oscillations may be a
result of the cyclic behavior of the applied current from the control algorithm, a
result of the material hardening and softening, or from an AC current component
imposed on the large DC signal as the power source does not provide a purely DC
signal.
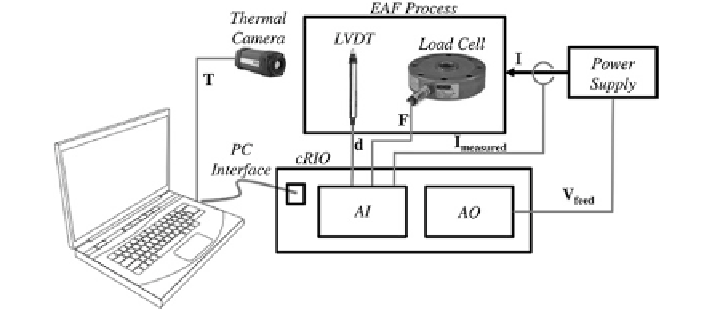