Civil Engineering Reference
In-Depth Information
Mechanical
Deformation
Modeling
Electrical Effects
Modeling
Thermal
Modeling
Mechanical Force Profile
Thermal Profile
Fig. 5.5
Coupled relations of EAM modeling [
13
]. The following modeling aspects specifically
contribute to the mechanical force profile, the thermal profile, or both. It is assumed that, from
the entire amount of electricity applied to the process, a portion contributes toward plastic defor-
mation, and the remainder contributes toward resistive heating, which increase the temperature of
the part and also contributes toward thermal softening
resistive heating of the workpiece.
P
def
is the magnitude of the reduction of the
required mechanical power to deform, due to the total applied electrical power.
Figure
5.6
shows that the magnitude of the thermal softening effect is highly
dependent on the specific metal being formed, as well as the actual temperatures
reached during the manufacturing process. Of note, in the thermo-mechanical
model, the material strength coefficient,
C
(
T
)
is adjusted to one constant value or
to a temperature-dependent profile representative of the temperatures reached for
specific EAF processes. As a result, the decrease in the force needed for the same
deformation as in a conventional test can be considered through two mechanisms:
Fig. 5.6
Tensile strength
versus temperature for
various metals [
14
,
15
].
Tensile strength versus
temperature profiles show
that the strength is reduced
by different magnitudes as
the temperature is increased
for Al6061-T6511, SS304,
and Ti-G5
1200
1000
Ti-G5
800
600
304 SS
400
200
Al6061-T6511
0
0
200
400
600
800
1000
Temperature (
o
C)
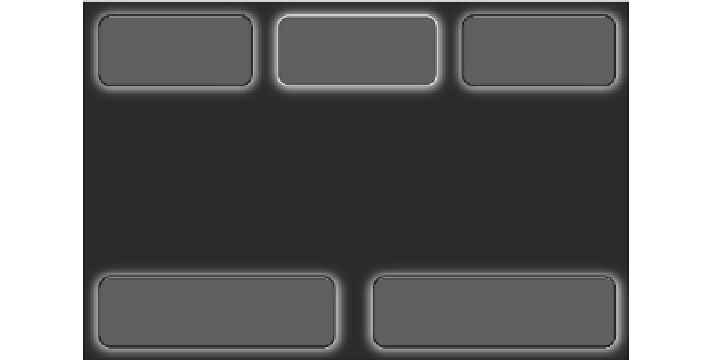

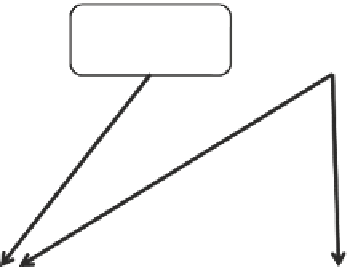
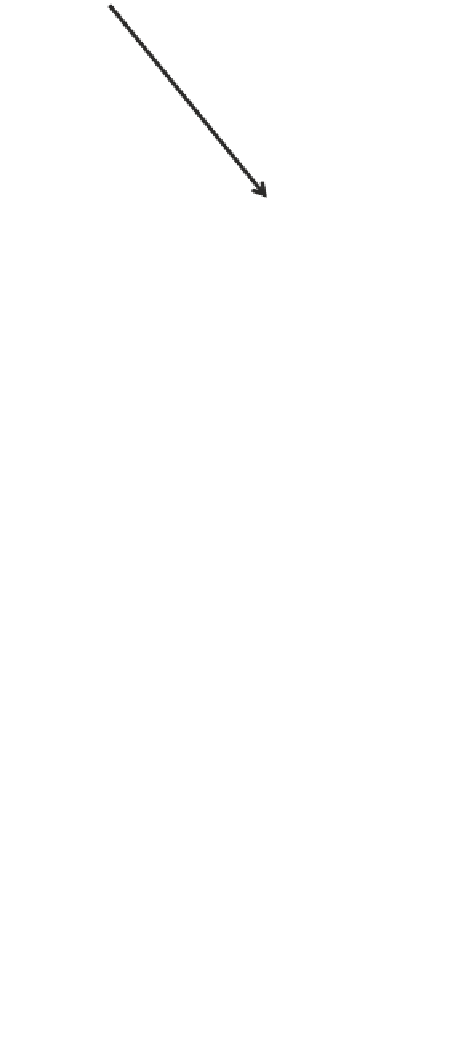
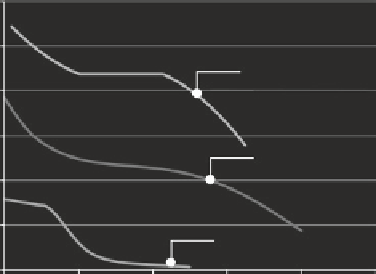