Civil Engineering Reference
In-Depth Information
The derivation begins by establishing expressions for the effective stresses
and strains acting on a plastically deformed billet without current in the classi-
cal cylindrical upsetting test using the upper bound analysis. This approach uti-
lizes key metal forming relations derived from works by Lange [
2
], Backofen [
3
],
Kobayashi et al. [
4
], Wagoner and Chenot [
5
]. The material is assumed to follow
the power law as shown in Eq. (
5.1
):
(5.1)
σ =
C
ε
n
where
σ
is the effective flow stress,
C
is the strength coefficient,
ε
is the effective
strain, and
n
is the strain hardening exponent. After the equations for stress and
strain are established, the next step is to include the effects of the electrical current
applied to the part, which takes place in the following section. Two aspects are
considered: (a) the applied electrical energy and (b) the electroplastic effect on the
material's behavior and on the efficiency of the process. The analytical model is
verified with results (force and position data) from EAM compression tests run on
Al6061-T6511 specimens, by Perkins et al. [
6
]. Finally, the potential applications
of the developed analytical model are discussed.
5.1.2 Analysis of an Electrically Assisted Compression
Process
An experimental schematic of an electrically assisted compression test can be seen
in Fig.
5.1
. A power source provides electricity and a variable resistor controls the
magnitude of current flowing through the dies. Insulation is placed between the
dies and the machinery, thus to ensure all electricity flows through the workpiece.
Electrons flow through the workpiece from anode to cathode; material flow is
p
Thermal
camera
Press
Power
source
Insulation
Temperature
measurements
Die
+
_
Workpiece
~
DAQ
System
V
Position and Force
measurements
A
p
Fig. 5.1
EAM compression test schematic. Main components include a controllable power sup-
ply, a thermal camera, and insulation placed between the dies
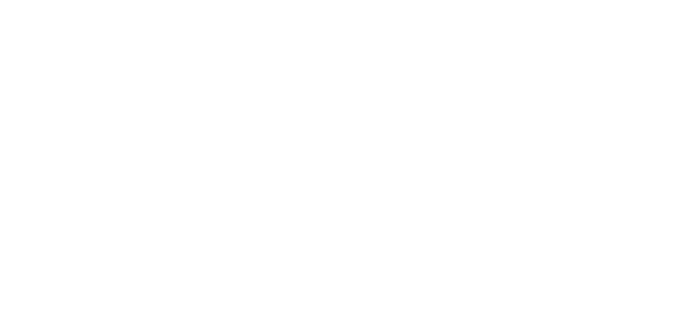
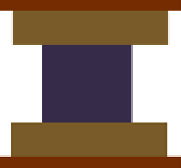


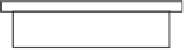

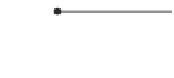




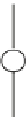
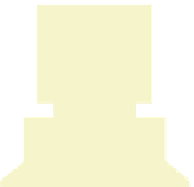



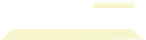
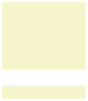
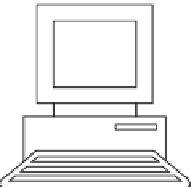






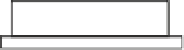

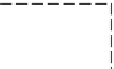

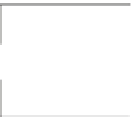