Environmental Engineering Reference
In-Depth Information
Parameters Calculated from Input Data
Description
Value
Units
Symbol
Design Wind Speed
10.50
m/s
V_design
50 year extreme wind speed
52.50
m/s
V_e50
50yr extreme tip speed ratio
1.93
n/a
λ
_e50
Design Tip Speed Ratio
6.77
n/a
λ
_design
Drive Train Efficiency
0.60
n/a
H
Design Torque
11.32
Nm
Q_design
Projected Area (turbine swept area)
2.96
m^2
A_proj
Design Rotational Speed of the Rotor
73.30
rad/s
ω
_n,design
Maximum Possible Rotor Speed
104.72
rad/s
ω
_n,max
Max Yaw Rate
2.99
rad/s
ω
_yaw,max
50yr extreme tip speed ratio
1.93
n/a
λ
_e50
Eccentricity of the Rotor Centre of Mass
4.85E-03
m
e_r
Effective brake torque
0.00
Nm
M_brake
Fig. 9.2
The second sheet of the SLM spreadsheet
The fifth chart in Fig.
9.5
gives the output of equivalent stresses. Figure
9.6
shows the sixth chart used to determine the material strengths for ultimate loading
and fatigue using the input information on material characterisation and number of
cycles to fatigue. It has been assumed that the materials for the blade and the main
shaft have not been properly characterised and so attract the highest partial load
factors from Tables
9.7
and
9.8
. The sixth chart completes the data entry.
The final chart in Fig.
9.7
shows the outcome of the SLM calculations in terms
of the safety of the relevant component (blade root or rotor shaft). The rotor shaft
fails load case B, whereas the shaft and the blades easily pass all other load cases.
A major part of the reason why the rotor shaft fails Case B is the inadequate
characterisation of its properties. The assumed yield stress of 250 MPa is much
lower than is usual for case-hardened steels often used for shafts. In any case, even
for this low value, being able to demonstrate proper characterisation would lower
the material safety factor from 3 to 1.1 and this alone would allow the shaft to pass.
9.7 Further Test Requirements
IEC 61400-2 mandates testing to determine or validate the design power, design
rotational speed, design shaft torque, and maximum rotational speed. In addition
the following are required:
• a blade static test, combining the highest centrifugal load with the largest
bending moment to test the integrity of the blade. The standard recommends
fatigue testing of the blade, but does not require it.
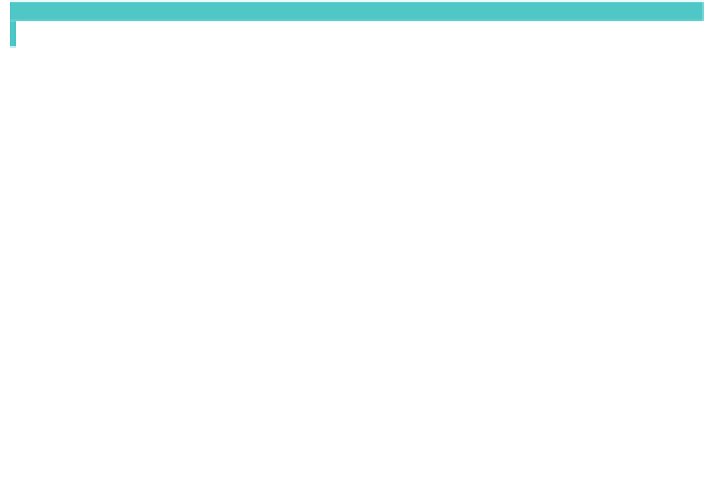







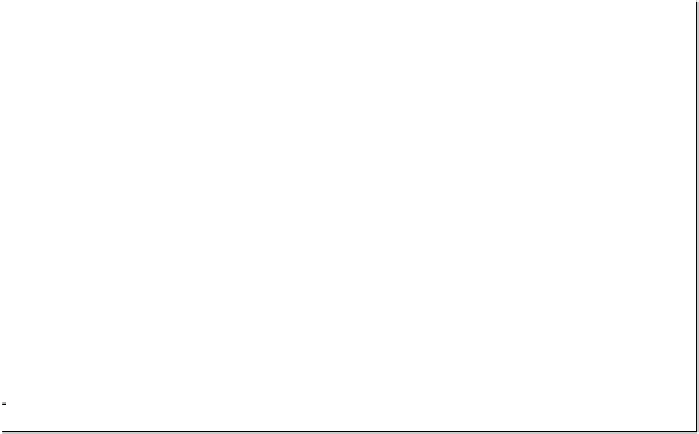












































Search WWH ::

Custom Search