Environmental Engineering Reference
In-Depth Information
TABLE A.10
Average Heat Efficiency (%) by Kind, Type and Scale of Industrial
Furnaces
Scale
Kind
Type
Small
Middle
Large
Average
Metals heating furnace
Continuous
38
45
55
46
Batch
10
33
42
28
Metals heat treatment furnace
Continuous
27
37
52
39
Batch
18
24
26
23
Aluminum-melting furnace
Batch
27
34
40
34
Average
Continuous
33
41
54
43
Batch
18
30
36
28
Average of continuous type and batch type
26
35
43
36
Total average
35
A.5 EFFECT OF ENERGY SAVING BY DEVELOPMENT OF
HIGH PERFORMANCE INDUSTRIAL FURNACES
A.5.1 A
SSUMPTIONS
OF
C
ALCULATIONS
The energy saving effect by the development of high performance industrial furnaces
was evaluated. The number of installed industrial furnaces, their energy consump-
tion, and the assumed values statistically obtained by this investigation are used.
1. Furnaces
The subject furnaces are the following 11 types of furnaces within the 19 types listed
• Melting furnaces (steel-melting furnaces, nonferrous and metals melting
furnaces, ceramics melting furnaces)
• Heating furnaces (metals soaking furnaces, metals heating furnaces)
• Heat treatment furnaces (metal heat treatment furnaces, surface heat treat-
ment furnaces, surface treatment furnaces)
• Ceramics baking furnaces
• Chemical industry furnaces
• Drying furnaces
The heat efficiencies of these furnaces are presumed to be as low as 35% on
averages excluding cement sintering furnaces and petroleum heating furnaces, which
are discussed in Section A.6.
Figure A.9
shows the relationship between the heating
capacities and the heat efficiencies obtained from the questionnaires for continuous
metal heating furnaces and heat treatment furnaces. According to the results of the
questionnaires, the recuperator, which is waste gas recovery equipment, is generally
installed in continuous metals heating furnaces. On the other hand, most metals
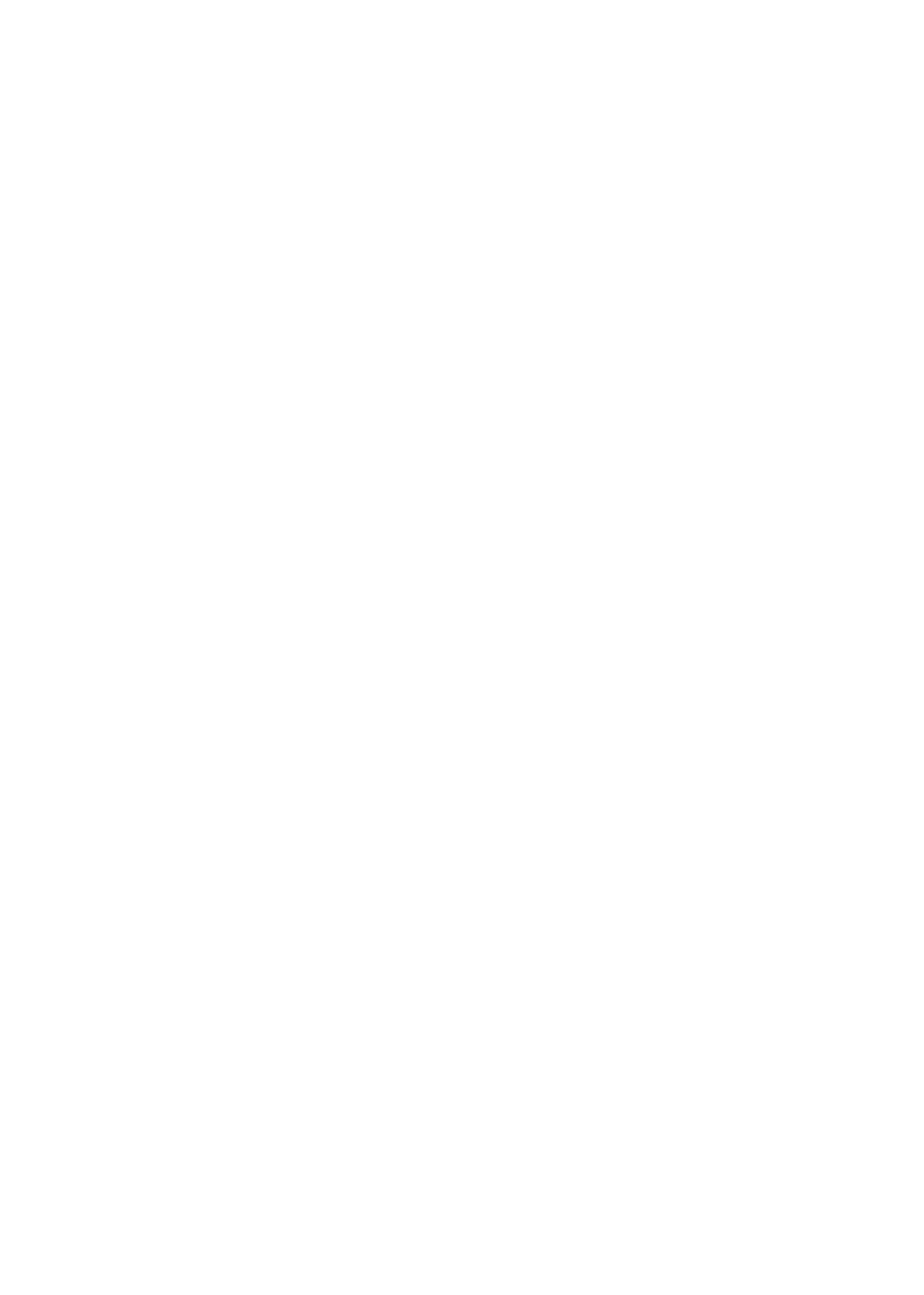



















Search WWH ::

Custom Search