Environmental Engineering Reference
In-Depth Information
(
a
)
(
b
)
(
c
)
Figure 35: Ship-based access to offshore wind turbines. Ships used: (a) WindCat;
(b) Aaryan; (c) Moidart.
vessels for wind farm support are small vessels with lengths between 14 and 20 m,
with either a single or a twin hull shape, and a bow section that is designed for
access. Safe access is provided by intentionally creating frictional contact between
the vessel and a boat landing structure on and in order to have no vertical vessel
motions at the point of contact. A rubber bumper on the vessel bow forms this
contact point; the thrusters push the boat against the structure to create the friction.
The boat now pivots around the bumper and personnel can step from the vessel
bow onto the turbine ladder safely. This method is generally being used for main-
tenance visits and applied by different types of vessels as shown in Fig. 35.
This ship-based access to offshore wind turbines is limited by wave conditions.
As wave conditions get rougher, ship motions will become lager and there is a
possibility that the vessel loses its contact with the boat landing. As a result, the
vessel can start moving relative to the offshore structure. In this situation, the
safety of the person accessing the turbine can no longer be guaranteed: the access
procedure is no longer safe. For this reason, access operations are limited to cer-
tain wave conditions. The general way of describing the limiting wave conditions
for access is by giving the limiting signifi cant wave height for an access method.
In wave conditions exceeding this limiting signifi cant wave height, the access
operation is considered too dangerous and will therefore not be performed.
6.1.3 Motion compensation systems: Ampelmann and OAS
The core of the problem when transferring people from a ship to a structure is that
the vessel moves with the waves and the structure is stationary. The development
of offshore wind sparked new innovations in this fi eld. Several systems have been
developed that compensate the wave motions partially or fully to remove the rela-
tive motion problem. The Offshore Access System is a hydraulic gangway that
compensates the heave motion while connecting to the offshore structure. The off-
shore structure needs to be equipped with a landing station where the OAS grabs
onto. As soon as the contact is made, the active compensation is switched off and
the gangway hinges passively on both ends, as shown in Fig. 36.
The Ampelmann follows a different approach: it cancels all motions in the 6 degrees
of freedom (surge, sway, heave, roll, pitch, yaw) to achieve a completely stationary
platform. A gangway is then extended that is lightly pressed against the structure to
allow quick and safe access. The additional advantage is that no landing station is

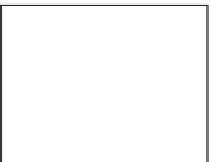

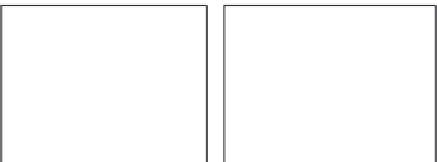
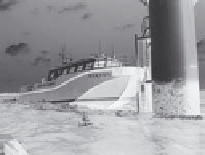
Search WWH ::

Custom Search