Environmental Engineering Reference
In-Depth Information
Branner
et al
. [58] recently investigated how well different FE modeling
techniques can predict bending and torsion behavior of a wind turbine blade. The
results from the numerical investigations were directly compared with measure-
ments obtained from experimental testing of a section of a full-scale wind turbine
blade. Torsional testing was performed by locking the tip cross section in a point
directly over the center of the box girder (see Fig. 18). This point is fi xed, but the
cross section can rotate around the
z
-axis and translate in the horizontal (
x
-
z
) plane,
since the vertical bar, indicated in Fig. 18, is able to rotate in both ends. The move-
ment in the horizontal plane is not entirely free since the movement is restricted to a
circular arc. The numerical and experimental results are in shown in Fig. 19.
y
z
x
T
Figure 18: Locked torsion of blade section. The vertical bar is able to rotate in
both ends. The cross section can rotate and is restricted to move along
a circular arc.
0
0.5
1
1.5
2
2.5
3
3.5
4
4.5
5
0
-0.005
-0.01
-0.015
Experimental data
Outer surface model
Mid thickness model
Shell solid model
-0.02
-0.025
-0.03
Spanwise distance (z-direction) [m]
Figure 19: The twist angle of the blade section (see Fig. 18) is shown as a function of
the distance from the root,
z
. The experimental results are shown as points
and the model predictions for various FE models are shown as lines [58].
















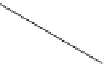







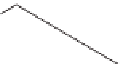










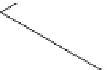








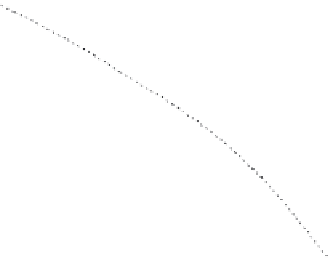














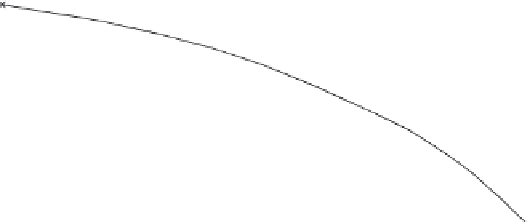







































































































Search WWH ::

Custom Search