Environmental Engineering Reference
In-Depth Information
L
Local wind velocity
Velocity due to blade
movement
a
D
Resultant air velocity
relative to blade
D
q
q
b
L
D
L
L
D
Figure 7: Plan view of velocity vectors and lift,
L
, and drag,
D
, vectors for a VAWT
with freestream velocity,
V
∞
, after Sharpe [ 23 ].
Kirke [25, 26] conducted an in-depth study of a number of three-bladed giromills
with aerodynamic/mechanical activation of the blade pitch mechanism. These
devices were referred to as “self-acting variable pitch VAWTs” with straight
blades. Each blade was mounted at its mid-span on the end of the rotor radial arm
and counterweighted so the mass centre coincided with the pivot axis, located
forward of the aerodynamic centre. The pitch mechanism was activated by the
moment of the aerodynamic force about a pivot, opposed by centripetal force act-
ing on a “stabiliser mass” attached to the radial arm, such that the aerodynamic
force overcomes the stabiliser moment and permits pitching before stall occurs.
Lazauskas [27] had previously carried out modelling of three different types of
blade pitch actuation mechanism and had predicted signifi cant improvement in
turbine performance compared to fi xed pitch VAWTs. Wind tunnel tests reported
by Kirke and Lazauskas [26] were carried out on a prototype rotor of 2-m diameter
and solidity
Nc
/
R
= 0.6 with three blades each 1.0 m long and with 0.2 m chord
and NACA0018 profi le. Comparison between the wind tunnel tests and numerical
results for various blade pitch scenarios were quantitatively good. Following these
laboratory tests a 6-m diameter demonstration turbine was built by Kirke with the
three blades being 2.5 m in length using the NACA0018 aerofoil profi le (Fig. 8).
Unfortunately, this device performed relatively poorly compared to theoretical
predictions. This was apparently due to: (i) high levels of freestream turbulence at
the test site, so that blades were subjected to variable wind speeds and the rela-
tively massive rotor was slow to respond to sudden gusts and lulls and therefore
operated well away from the optimum tip speed ratio most of the time; (ii) low
wind speeds and therefore relatively low blade Reynolds number; (iii) high parasitic
drag losses.

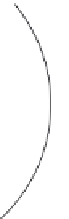





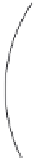


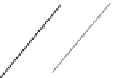













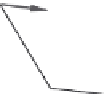




































































































































































































































Search WWH ::

Custom Search